Raffinerie Heide rethinks energy management
Energy usage as a key management factor in production
North German Raffinerie Heide, a manufacturer of fuels, heating media and products for the petrochemical industry, is reliant on particularly energy-intensive processes in its processing of hydrocarbons. In the light of the intensifying price trends on the energy and CO2 certification market, the management board has decided to join forces with the Horváth expert team to analyse its energy management from top to bottom and enhance its improvement potential, thereby significantly reducing its energy costs – and, last but not least, making its production more environmentally friendly.
The developments on the energy market that have been set in train by the energy transition and amplified by Russia’s war of aggression against Ukraine are affecting the energy-intensive process industry so severely that energy savings and the associated improvements in efficiency are no longer just sound economic policy but, given the current energy supply situation, have become the decisive management factor. The exorbitant costs are forcing companies to act. The best-practice example of new energy management at Raffinerie Heide shows how strategic and operational considerations result in significant improvements – in respect of both the costs as original economic factor as well as CO2 emissions and the associated issue of public reputation.
CURRENT PRICE TRENDS CANCELLING OUT MARGINS
Natural gas is a key energy source that is required at Raffinerie Heide for the provision of electricity and process heat. Due to the dynamic market trend, natural gas prices in the first quarter of 2022 crossed the threshold of 100 euros per megawatt hour, thereby surging to three to four times the average level of previous years. In a parallel development, the prices for CO2 certificates increased from 20 to over 80 euros per tonne of CO2 emissions. Both price trends are having a major impact on the refinery’s margins.
HORVÁTH EXPERTISE AS THE GUARANTEE OF CONCEPT-BASED ENERGY MANAGEMENT
By calling on the experts from Horváth, Raffinerie Heide brought additional know-how into the firm with the aim of jointly raising energy usage management up to a level that will be viable in the long term. The starting point was the Solomon benchmark used across the refining industry that permits anonymous comparison with the competition: Based on the Energy Intensity Index (EII) and internal energy consumption figures, the project team determined the status quo and defined the new target range. To achieve the savings target, the team worked out and initiated, on the one hand, strategic measures in the form of energy-efficient investments in the site. On the other, they identified optimization potentials that required no investment and were directly effective, and realized them by adapting plant operation systems under production conditions.

THE TWIN PILLARS OF THE NEW ENERGY MANAGEMENT
The sustainable investment perspective was covered by the program’s first pillar: strategic energy management. Based on a top-down analysis, promising investment projects were identified and evaluated. For each project, the team of experts scrutinized a specific business case with price trends and funding options and analyzed both potential and feasibility. The evaluation was based on previously defined criteria and served as the basis for the introduction of potential solutions into the program.
The second pillar of the program covered operational energy management. To secure the maximum level of expertise, cross-functional energy management teams consisting of process engineers, advanced process controllers, production specialists and refinery experts from Horváth were set up. An agile approach to the task sharpened the focus and accelerated the implementation to the required speed. The optimal team was determined for each system-specific sprint. Based on production data, statistical evaluations were carried out to identify dependencies and find new states of equilibrium in respect of energy usage. Previously determined optimization measures were validated by operational trials. Once the optimizations had been confirmed in practice, the new insights and findings were firmly anchored in the production system. With this approach, measures were established in the organization for the long term.
EFFICIENT PROGRAM MANAGEMENT AND TECHNICAL EXPERTISE GUARANTEED SUCCESS

Horváth established an ongoing program management system adapted to the multiplicity of projects, by means of which all measures and projects from both program pillars converged on one single joint management system. This made it possible to efficiently manage the abundance of individual factors and monitor the status of all measures. It also allowed the clear and manageable coordination of the impacts of different operational areas and the setting of targeted priorities. By imposing and adhering to a system of program governance, Horváth was able to guarantee progress. Raffinerie Heide was thus able to draw on sound and transparent results to make the decisions required for long-term viable energy management. Not only that, but the availability of Horváth experts in the system-specific sprints also guaranteed an outside-in view and new food for thought.
SECURING SUSTAINABLE RESULTS
In collaboration with the Horváth team, Raffinerie Heide was able to anchor energy management as a strategic element even more securely in the organization. The company managed to make significant savings even before the project was concluded. The success which quickly became apparent motivated the project team to plan further improvement measures and gave the project as a whole and all those involved in it the required visibility in the organization. The results achieved contributed to both the economic and ecological goals.
Energy savings and the associated improvements in efficiency are no longer just sound economic policy but, given the current energy supply situation, have become the decisive management factor. Raffinerie Heide therefore decided to put the existing energy management system to the test and to realign it with a new conceptual framework.
INTERVIEW
MR. BEHRENS, WHAT IN YOUR VIEW WERE THE PROJECT’S SUCCESS FACTORS?
Thanks to the comprehensive support of Horváth – from the analysis and goal setting through to program development and implementation – our experts were free to focus one hundred percent on their own strengths. The project governance brought in and the project management also allowed us to use metrics to follow the achievement of our goals. The perspective from outside was especially valuable. We benefited from the fact that the Horváth refinery experts questioned old thought patterns, allowing us to follow new approaches.
WHAT WERE THE ADVANTAGES OF THE OPERATIONAL ENERGY MANAGEMENT TEAMS?
Cross-functional teams queried the existing limit values that were blocking the optimization of our energy usage and put them to the test. Adapting the plant operation systems enabled us to exploit CAPEX-free potentials. The coaching offered by the Horváth refinery experts introduced our staff to new methods for identifying and realizing new savings potentials.
WHAT WERE YOUR PERSONAL HIGHLIGHTS DURING THE PROJECT?
By adapting return flow conditions in columns or reducing oven temperatures, we optimized the energy consumption of individual systems without needing to make major changes to product exploitation structures. These kinds of savings were very quick to implement, at no expense and with long-term success to boot.
WHAT ARE THE NEXT STEPS?
Together with Horváth we’re going to fill our program for the long term with projects and measures to ensure that we achieve our energy management program goal by 2030. This will allow us to stay competitive in the market.
About Raffinerie Heide
Raffinerie Heide GmbH is Germany’s northernmost crude oil refinery. On a site measuring 134 hectares, the company processes some 4.5 million tonnes of crude oil per annum. A good 70 percent of the crude oil is used to make fuel. A significant share of the petrol and diesel used in Schleswig-Holstein thus comes out of the company’s refinery. Raffinerie Heide also makes aviation fuel, the bulk of which is supplied to Hamburg Airport. Alongside fuel production, the refinery in Hemmingstedt also produces roughly 450,000 tonnes of petrochemical products annually.
Read here how we can support you in successfully decarbonizing your business model.
Your Contact
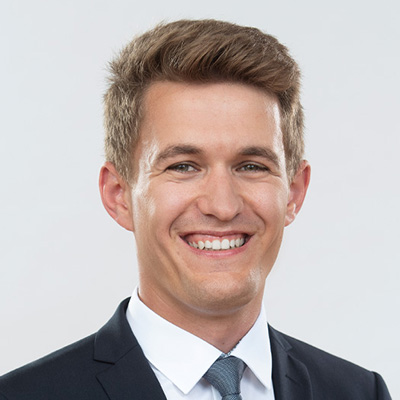
Jonas Schulze