If automotive supplier ZF Friedrichshafen were suddenly no longer able to supply the 8-gear automatic transmission, production lines at a number of automotive companies would quickly come to a standstill. In order to prevent this worst-case scenario, experts from Horváth & Partners assessed ZF’s complex supply chain for risks, and developed measures to make it more robust.
The supply chain for a product is as complex as the product itself. Within the automotive industry, for example, a single vehicle draws on countless suppliers around the globe, each of which in turn works with its own suppliers. If just one link in the chain breaks, production delays and serious financial damages may be the result. The risk is especially high in the case of single-source supply, when the required part can only be provided by one supplier. However, even a supposedly secure supply that is covered by multiple suppliers may harbor unexpected risks if these suppliers all use the same upstream supplier, or if they have not implemented sufficient safeguards.
THE GOAL: 100% SUPPLY SECURITY
“There are few automotive components as complex as a modern automatic transmission. Certain individual products require a wide range of components from more than 100 Tier 2 suppliers,” explains Stefan Bultmann, who is responsible for risk management at the Horváth & Partners Automotive Center. Because of this complexity and the very high quality of the product, the 8HP automatic transmission is supplied by ZF Friedrichshafen AG to a large number of OEM customers, on a single-source supply basis. In order to prevent a situation in which ZF – which, with a purchasing volume of €20 billion and sales of almost €37 billion is now the second-largest Tier 1 supplier in the industry – would be unable to deliver this crucial product, the automotive supplier commissioned Horváth & Partners with developing an efficient, holistic Supply Chain Risk Management (SCRM) system. The goal was to guarantee 100% supply security, taking efficiency and cost awareness into consideration at the same time. A collaborative approach also needed to be applied for the integration of the supply chain, and a standardized method developed that could be applied to the entire supplier base for use as a toolbox for future rollouts.
SUPPLY RISK COMPARABILITY
ZF first worked with the experts at Horváth & Partners to identify potential risks. “We mapped the supply chain as far as Tier 2 and 3 suppliers in order to gain a clear view of upstream suppliers and material flows,” reports Stefan Bultmann. To this end, all components of the automatic transmission were analyzed and evaluated across nine risk categories: Nature, production processes, IT infrastructure, finances, sabotage, fire and explosion, logistics and inventory, security and politics, media supply. They were then weighted according to three factors.
At the end of this process, the Risk Assessment Indicator (RAI) presented a standardized figure for risk identification. In particular, this methodology offers a robust means of comparing breakdown risk for various suppliers. The experts from ZF and Horváth & Partners then identified which 15 of the company’s many suppliers were most important in this context.
In particular, the Risk Assessment Indicator facilitates a robust method for comparing various suppliers.
SENSIBLE PRIORITIZATION, NOT AD HOC MEASURES
Following the analysis, the project team sought out appropriate preventive measures that would eliminate or reduce risks in the supply chain. Alongside simple ideas such as introducing continuous monitoring for various risk aspects, these also included the preparation of emergency plans with clearly defined responsibilities, and technical solutions for early fire detection. The processes were tested and refined at the ZF factory in Saarbrücken and at a number of supplier sites; another important requirement was ensuring a broad understanding of risk management among the Executives of the various suppliers. Tier 3 suppliers were also involved in developing the solution and worked actively to help do so. “Everyone involved was aware of the importance of the topic, and the feedback on the process was extremely positive across the board,” emphasizes Bultmann.
As well as the project being a complete success for ZF Friedrichshafen, it also resulted in a win for Horváth & Partners in the 2018 Best of Consulting prize awarded by German business news magazine Wirtschaftswoche. “The tools used and tested have produced an efficient toolbox, which can also be applied very effectively to other supply chains. The methods represent an interdisciplinary refinement of SCRM,” explains Jochen Kröber, Head of Supply Chain Management, Production & Development at Horváth & Partners. Indeed, discussions are already under way as to whether the project could serve as the basis for a SCRM standard that is certified by the German Association of the Automotive Industry (Verband der Automobilindustrie/VDA).
Your Contact
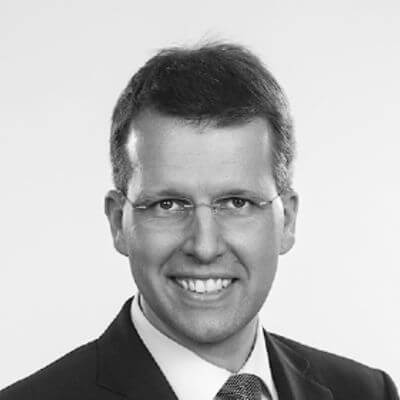
Stefan Bultmann
More articles
Study
Digital Value 2019

Supply Chain Risk Management at ZF Friedrichshafen
Interview with Dr. Michael Karrer, Head of Supplier Management at the ZF Group
