Transferring digital technologies and management approaches from the industrial sector is a key that allows service companies and units to provide their services more efficiently and more effectively. Operations Performance Management 4.0 from Horváth & Partners supports organizations in doing just that.
Digitization is driving the further development of business processes within companies in all sectors. Smart networking in the manufacturing industry is progressing particularly far under the buzzword Industry 4.0. The new technologies also offer huge potential for the service provision, whether in shared services centers for back-office processes, or in the operations centers of banks and insurance agencies.
INDUSTRY AS A MODEL
Organizations are coming under pressure to act due to growing cost and competitive pressure, as well as new and changed requirements from customers, who often expect instant responses from service centers in light of the digital communications channels in use. However, digital technologies alone are not enough to provide services more efficiently and more effectively. Operations Performance Management 4.0 (OPM 4.0) offers support in this regard.
OPM 4.0 allows for efficient
effective service provision
in the digital age.
The approach takes into account all the key service provision tasks with the goal of fulfilling the requirements of customers and internal clients in terms of the agreed service level. This includes both the service provision process and its planning and steering. Based on the Industry 4.0 model, the concept adapts planning and management approaches from the industrial production sector to the specific requirements of service units. The new technical possibilities available are utilized to digitize the creation and management of services.
DIGITAL PLATFORM AS A VIRTUAL PRODUCTION LINE
Digital process and service architecture plays a key role in this process. It allows products, services, process steps, the underlying IT and the necessary skills of employees and units to be considered as integrated elements. In addition, it forms the basis for the planning, transactional and management components of OPM 4.0. The consistent E2E view plays a decisive role in this process, since it allows all necessary processes to be designed optimally and digitized as effectively as possible from a customer perspective. The process steps of all units involved, including the robot technologies used, are described appropriately and documented with the necessary skill levels and time requirements for each, in a manner reminiscent of a work plan for use in the industrial manufacturing sector.

The core of OPM 4.0 involves connecting process and IT architecture – similarly to established platform strategies in the industrial sector. As part of this approach relevant, standardized process components are mapped as reusable IT components within an integrated platform, based on the “Lego principle”. This platform functions as a virtual production line, serving processes, employees and customer requests at the same time.
RESOURCES AND ORDERS UNDER CONTROL
The comprehensive planning and steering of all resources is centralized – since this is the key to consistently high productivity. With OPM 4.0, the service products to be generated are planned on the basis of quantities over the course of time, and also based on cycle times. With the aid of rolling planning and opportunities for flexibilization – a result of using robot technologies – the required resources can be adjusted to the expected product quantities right up to the start of production. Furthermore, fine control of resource utilization allows for effective productivity management. Thanks to new, digital technologies, this planning logic can be implemented significantly more effectively, for example by means of predictive planning when forecasting product quantities.
Optimal management of incoming orders forms the basis for service production. In this regard, OMP 4.0 distinguishes between customer orders and the production orders and processes necessary for the provision of services. From the customer’s point of view, the focus is on fulfilling orders within an expected period. From a production perspective, however, it is also important to ensure that resources such as employees, robots and service providers are utilized as efficiently as possible. Both aspects are managed with the aid of workflow systems using the smart logic documented in these systems.
IMPROVE PERFORMANCE, BOOST POTENTIAL
Integrated performance management allows potential to be realized across the board. Real-time reporting of order status data, which usually originates from the workflow system, is aligned with information on the availability and utilization of resources on an ongoing basis. With the help of process mining, the quality of the defined processes is analyzed and continuous process improvement (CPI) is institutionalized.
In addition to the technological possibilities, people also play a role critical for success. Those at management levels, in particular, must recognize the added value of number-based management support, and must drive its implementation and acceptance among their employees.
This is certainly worthwhile, as a recent study by Horváth & Partners shows. The study reveals that, although the approaches used by OPM 4.0 are still a future consideration for most companies, some service providers are already enjoying considerable benefits from them. These are taking advantage of the possibilities offered by OPM 4.0 to provide their services more efficiently and more effectively in the digital age.
Your Contact
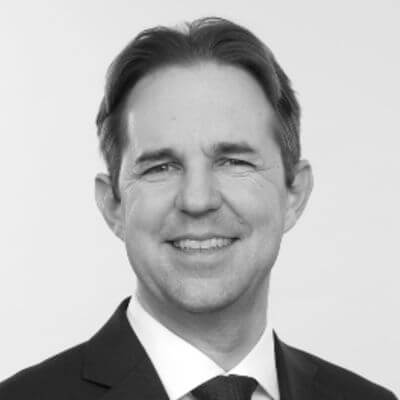
Markus Brenner
More articles
Interview with Gülabatin Sun, Deutsche Bank
"Robots drive productivity"

Interview with Anja Krusel, Borealis
„We need an e-culture."
